
BOOSTER for Z21PG by DF
License
:Public Domain
Description
Double DCC booster for train models, from N scale to O scale. High current driving capability thanks to two integrated circuits based on MOSFET half bridges (BBTN8962). All the user settings can be entered using a mechanical encoder, one push-button and one 1 inch wide OLED display. Hereafter the booster main features:
- Rated current driving capability of 30 + 30 Ampere, derated 10 + 10 Ampere
- Active cooling with temperature check of each output bridge
- Aluminum heatsink secured to the booster PCB and in thermal contact with MOSFETs using a silicone pad
- RAILCOM cutout propagation
- User selectable short circuit protection thershold current independent for each output
- Temperature monitoring for each output power stage
- Power supply under-voltage and over-voltage monitoring
- Double protection system at component level (BTN8962 - undervoltage, short circuit, over temperature) and at booster level (overall PCB temperature and output current). Specific protection with output diodes for inductive load driving.
- 1" OLED display for real time monitoring of:
- output current
- power stage temperature
- power supply voltage
- short circuit detection threshold
- RAILCOM cutout input and output
- Multi input capability to interface all the digital station or boosters
- XpressNet to interface directly the ROCO Multimaus and Lokmaus with one master and one slave port (ROCO 10764 and similar emulation). Overcurrent feedback to the Maus.
- LocoNet to interface the "LocoNet B" bus using the railsync signal to generate the DCC output. Overcurrent feedback sent to the LocoNet with specific broadcast signal.
- CDE input for generic DCC station with the overcurrent feedback on the "E" pin.
- All user parameters setting with a single incremental encoder and integrated push/push key (EC11) for emergency stop/restart and user parameters confirmation
- Red/Green LED to show the booster status (displayed on the user knob)
BOOSTER USER GUIDE
The booster has two main functionning modes:
1. DCC output. This mode is the normal functioning of the booster. Accepts one DCC in input (from XpressNet, LocoNet or CDE) and outputs an amplified copy of this signal. If the RAILCOM cutout is present in input, the RAILCOM cutout is replicated in output. The user display shows the following informations:
I1 / I2: output current (in Ampere) for the two boosters
T1 / T2: power stage temperature (in °C) for the two boosters
S1 / S2: functionning status for the two boosters
V: Boosters power supply voltage
P: Boosters power output (in W)
The "Booster Status" S1 / S2 can be as following:
RUN: the DCC output signal is generated, everything is OK
NDCC: DCC output inactive, there's no DCC in input
STOP: output inactive because the user pressed STOP key or sent a STOP command
OV.C: output inactive, overcurrent on this output
OV:T: output inactive, overtemperature on this output
OV.V: output inactive, power supply over voltage
UN.V: output inactive, power supply under voltage
2. User parameters setting. In this mode (activated pressing for more than 2 seconds the user knob) the user can adjust all the booster setting parameters. The user display shows the following informations:
The user can move accross the parameters using the knob and select one of them pressing the key when the parameter name is displayed in inverse (first row of the display). After the parameter selection, the user can change the parameter itself with the knob and confirm the value with the key. pressing for more than 2 seconds the user knob the booster will return in the "DCC Output" mode.
The user parameters table is the following:
Parameter | Default | Range | Remarks |
MAXCURR1 (A) | 5.0 A | 1.0 - 9.9 A | Overcurrent threshold for booster output 1 |
MAXCURR2 (A) | 5.0 A | 1.0 - 9.9 A | Overcurrent threshold for booster output 2 |
DELAY1 (ms) | 10 ms | 1 - 99 ms | Delay for overcurrent protection for output 1 intervention |
DELAY2 (ms) | 10 ms | 1 - 99 ms | Delay for overcurrent protection for output 2 intervention |
REARM1 (s) | 1 s | 0 - 9 s | Rearm time after overcurrent on output 1. Set to zero to disable the feature. |
REARM2 (s) | 1 s | 0 - 9 s | Rearm time after overcurrent on output 1. Set to zero to disable the feature. |
MAXTEMP1 (°C) | 90 °C | 30 - 99 °C | Maximum temperature for output 1. |
MAXTEMP2 (°C) | 90 °C | 30 - 99 °C | Maximum temperature for output 2. |
FANON (°C) | 45 °C | 30 - 99 °C | Activation temperature for fan cooler. Valid for both output 1 and output 2. |
FANOFF (°C) | 40 °C | 30 - 99 °C | Deactivation temperature for fan cooler. Valid for both output 1 and output 2. |
MIN VSUP (V) | 14 V | 10 - 24 V | Minimum voltage for booster power supply. |
MAX VSUP (V) | 18 V | 10 - 24 V | Maxmum voltage for booster power supply. |
CURRZERO1 (A) | 80 | 60 - 100 | Result of zero current calibration for output 1. |
CURRZERO2 (A) | 80 | 60 - 100 | Result of zero current calibration for output 2. |
CURRSPAN1 (A) | 4.0 A | 1.0 - 9.9 A | Span current calibration for output #1. |
CURRSPAN2 (A) | 4.0 A | 1.0 - 9.9 A | Span current calibration for output #2. |
CURRFACT1 (%) | 100 % | 70 - 130 % | Result of span current calibration for output #1. |
CURRFACT2 (%) | 100 % | 70 - 130 % | Result of span current calibration for output #2. |
BOOSTER CALIBRATION
The current pick-up, internal to the BTN8962 IC need to be calibrated for zero current (offset) and span (gain). The zero calibration is performed with the following steps:
1. Unconnect the DCC input signal
2. Unconnect any load from the outputs
3. Select on the menu CURRZERO1 or CURRZERO2
4. Press the key. In few milliseconds the value on the screen will be updated.
The span calibration is performed with the following steps:
1. Connect the DCC input signal
2. Connect one known load to the output1 or output2. For example with a power supply of 15V, apply one load of 3 Ohm (5.0 A output current)
3. Select on the menu CURRSPAN1 or CURRSPAN2
4. Press the key and adjust (to 5.0 A for the example) the expected current level using the knob
5. Press again the key. In few milliseconds the value on the screen (CURRFACT1 or CURRFACT2) will be updated. This value contains the correction (in percentage) to be applied to the current reading.
LED signaling
One red-green LED has been embedded on the panel PCB and the light is visible through the knob. The colors for the LED signaling are the following:
GREEN: DCC output active on both outputs.
BLINKING GREEN: no DCC signal on the booster input
ORANGE: Overcurrent condition on one or both outputs (with re-arm)
BLINKING RED: all remaining over limits conditions
OFF: configuration menu.
BOOSTER parts
The following is the list of the parts needed for the building of one 10 + 10 Ampere booster. Is it possible to find detailed instruction about the booster assembly in the "Project Attachments" section.
(4): 12 poles JST ZH (1.5mm pitch) female to female cable
(5): 40x40x20mm heatsink + 24VDC fan cooler with 2 pin connector (2.54mm pitch)
(6): 40x40mm heat conductive mat (1mm thick)
(7): Two 17.6mm plugs with springs
(8): 4 x M2.5 x 5 black nylon screws
(9): 4 x M2.5 x 5 x 1 black nylon washers
(10): 4 x M2.5 x 6 black nylon spacers
(12): 0.96" OLED display with I2C interface
(13): 4 x M2.5 black nylon bolts
(14): PLC04 enclosure (145x90x4mm)
BOOSTER firmware
The firmware for the open source 10+10 Ampere booster has been developed on the ARDUINO platform, based on the ATMEGA328P processor. The complete sorce code can be found at this link.
Design Drawing
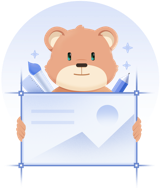
BOM
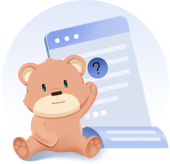

Project Members
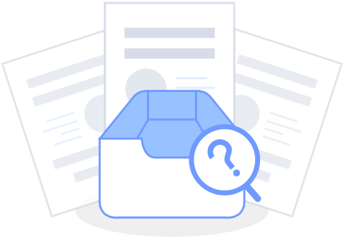
Comment