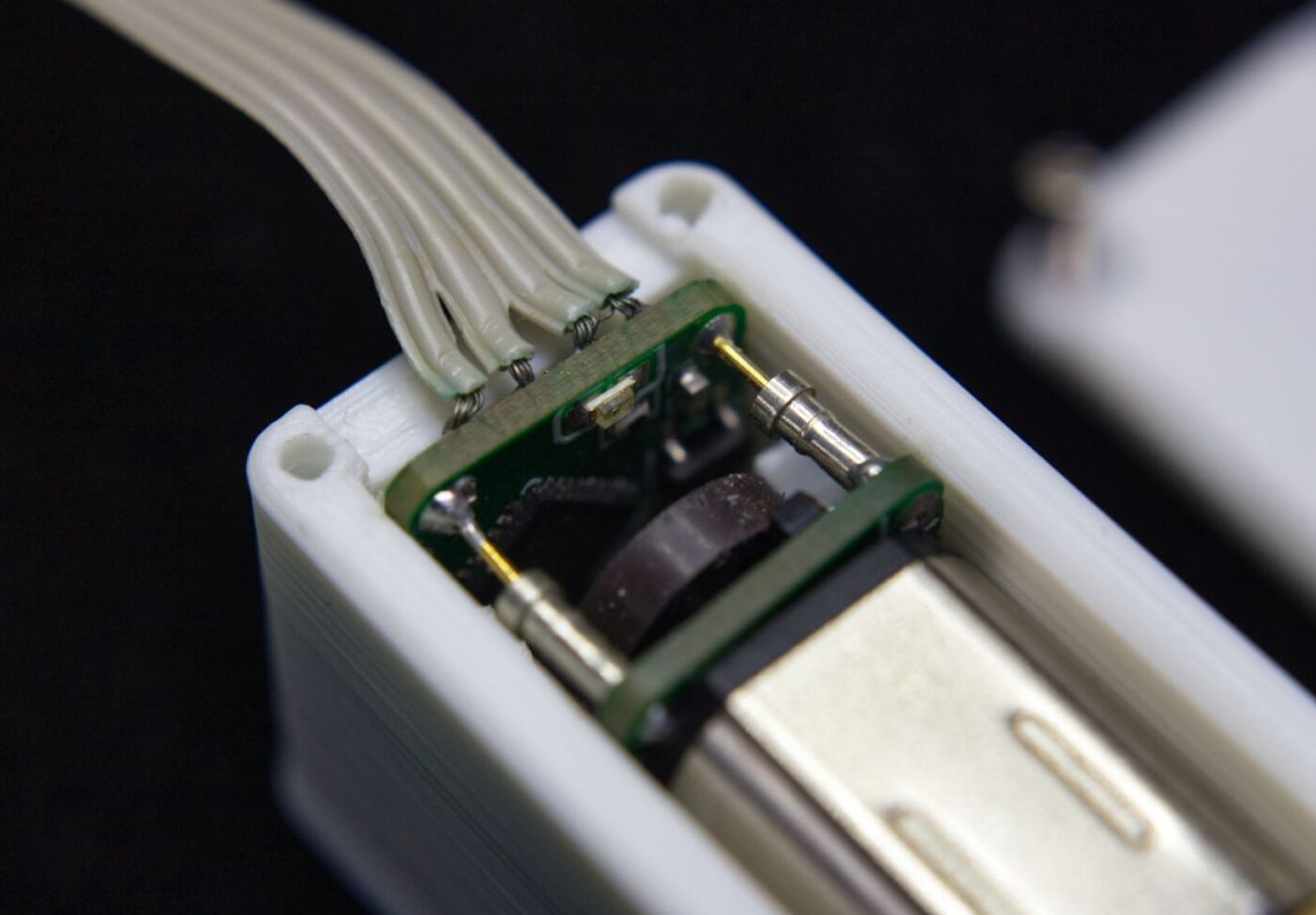
XMoto STM32
STDXMoto STM32
2.0k
0
0
0
Mode:Full
License
:CC-BY-NC 3.0
Cloned fromXMoto STM32 (stacked)
Creation time:2020-12-04 16:50:29Update time:2022-01-22 14:13:07
Description
Design Drawing
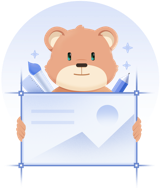
BOM
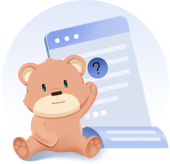

Add to Album
0
0
Share
Report
Project Members
Followers0|Likes0
Related projects
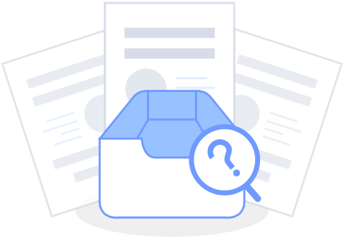
Comment