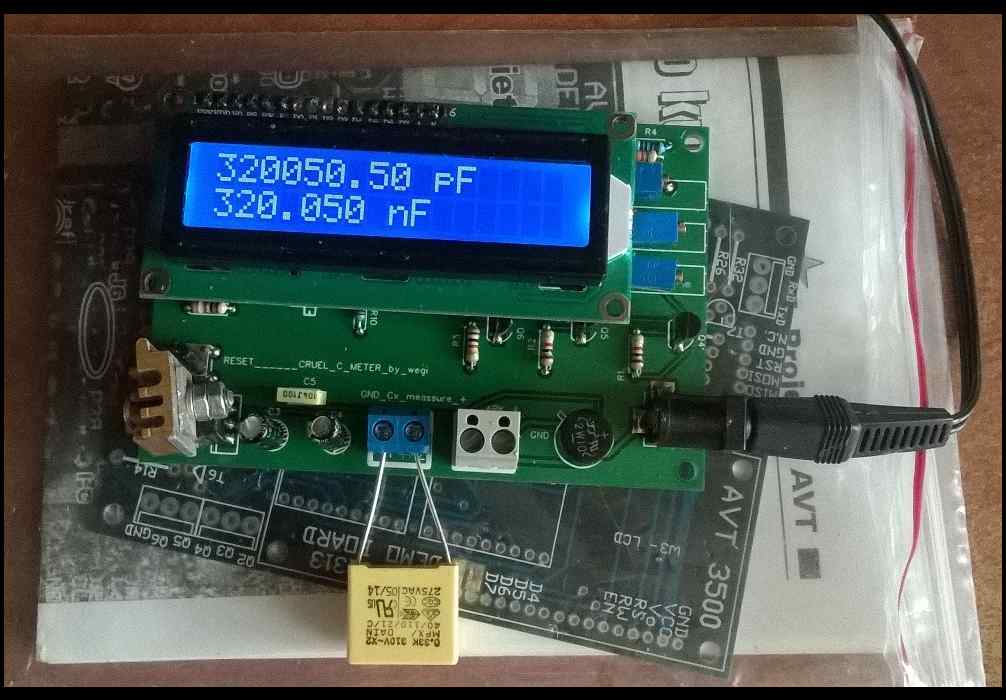
C_meter ATtiny2313
STDC_meter ATtiny2313
11k
0
0
2
Mode:Full
License
:Public Domain
Creation time:2016-03-22 20:38:13Update time:2021-06-08 09:14:55
Description
Design Drawing
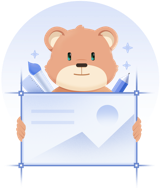
BOM
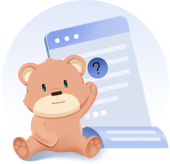

Add to Album
0
0
Share
Report
Project Members
Followers0|Likes0
Related projects
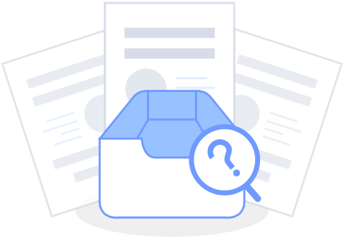
Comment