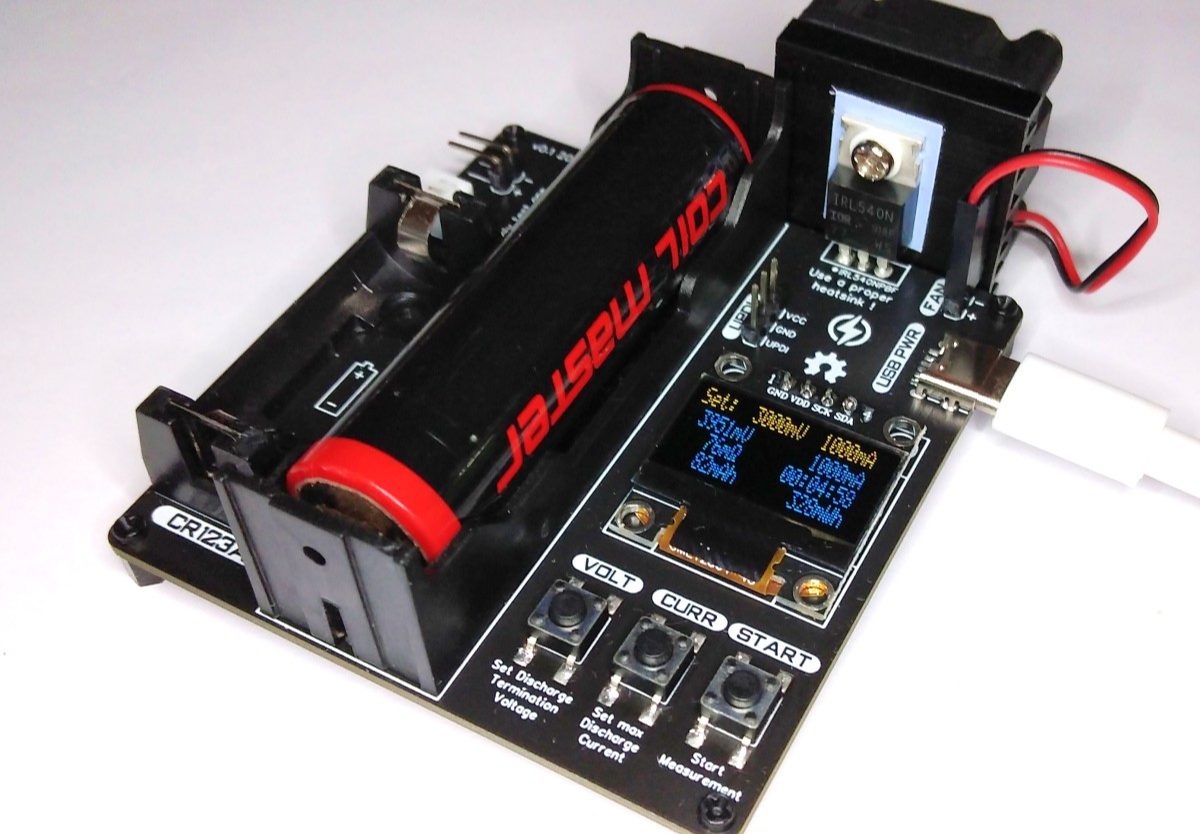
ATtiny412 BatteryCapacityTester
STDATtiny412 BatteryCapacityTester
2.3k
0
0
4
Mode:Full
License
:CC-BY-SA 3.0
Creation time:2022-08-01 18:56:06Update time:2022-08-20 08:06:49
Description
Design Drawing
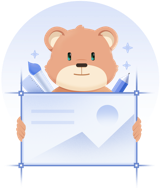
BOM
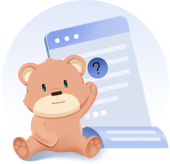

Add to Album
0
0
Share
Report
Project Members
Followers0|Likes0
Related projects
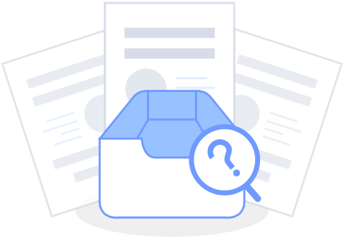
Comment