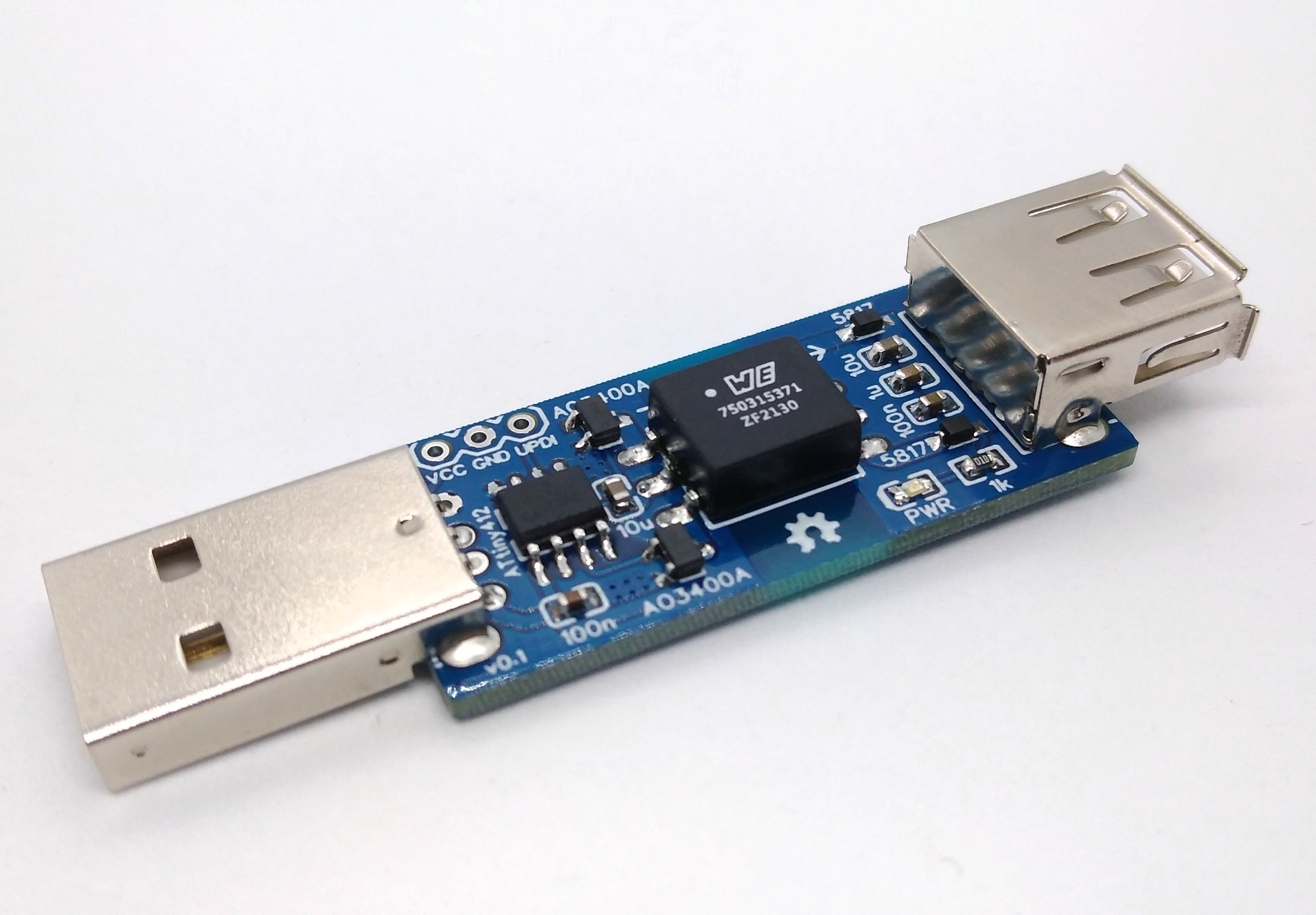
ATtiny412 5V Isolated DC/DC Converter
STDATtiny412 5V Isolated DC/DC Converter
1.2k
0
0
0
Mode:Full
License
:CC-BY-SA 3.0
Creation time:2022-08-27 13:16:21Update time:2023-09-26 12:38:56
Description
Design Drawing
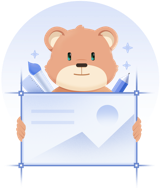
BOM
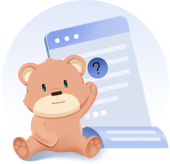

Add to Album
0
0
Share
Report
Project Members
Followers0|Likes0
Related projects
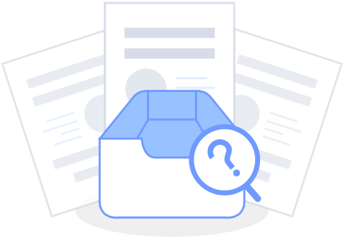
Comment