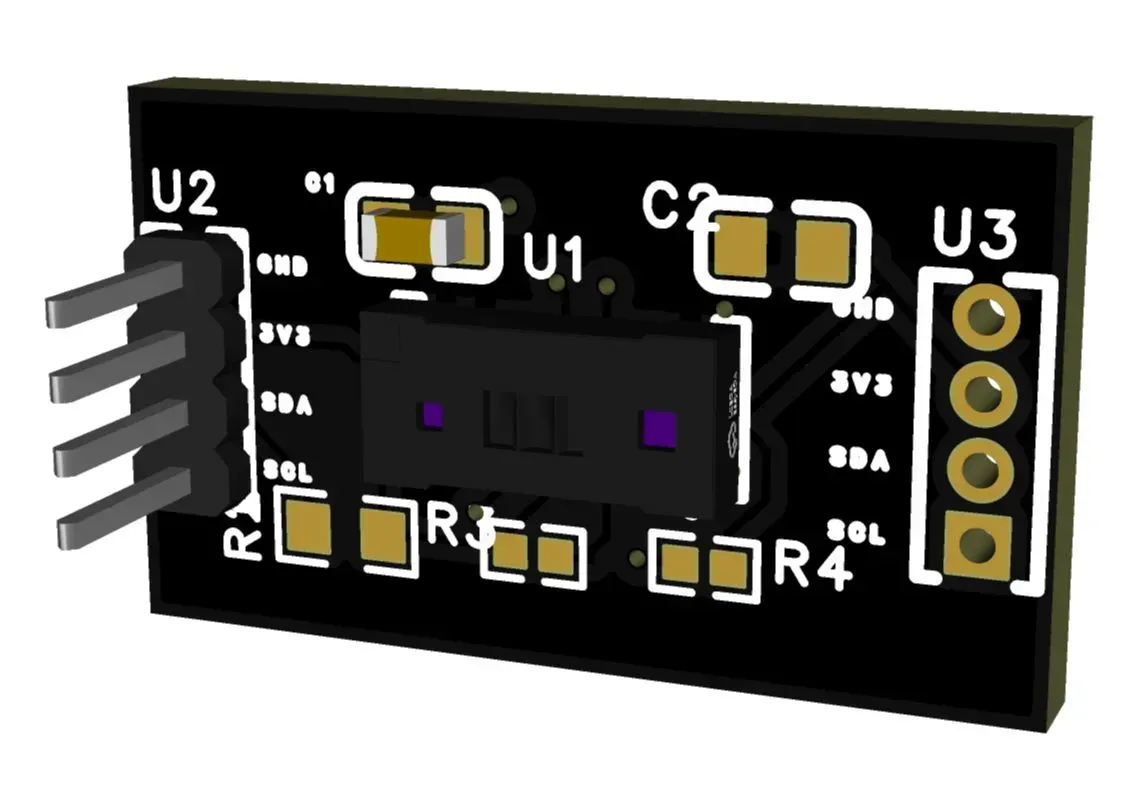
Miniature Lidar VL53L5CX
License
:CC BY-NC-SA 4.0
Description
Pushing the Limits of Miniature LiDAR: A High-Performance VL53L5CX-Based System
Making high-performance LiDAR smaller is tough—precision and size usually don’t get along. But we decided to challenge that. Meet our miniature LiDAR system, powered by the VL53L5CX sensor from STMicroelectronics. What makes it special? It’s compact, but thanks to a carefully designed 8-layer PCB and a 1.27mm pitch header, it still delivers rock-solid signal integrity. In other words, we packed serious performance into a tiny footprint.
Engineering Feat: Why 8 Layers?
The necessity of an 8-layer PCB isn't just for show—it's a critical design choice. When working at such a small scale, electromagnetic interference and signal degradation become major hurdles. To deal with this, dedicated ground and signal planes are strategically placed within the stack-up, ensuring noise suppression and optimal performance. The result? A LiDAR system more compact than anything seen before, yet delivering unparalleled accuracy.
Development Process: From Concept to Reality
Designing such a compact LiDAR system required careful planning and iteration. We started with an initial 4-layer prototype, but excessive noise and poor signal integrity led us to refine the design further. The transition to 8 layers allowed us to implement dedicated shielding and controlled impedance traces, solving previous issues while maintaining a minimal footprint.
To ensure compatibility with various embedded systems, the PCB was designed with a 1.27mm pitch header, allowing it to be easily integrated into existing hardware platforms without bulky connectors. Extensive simulation and real-world testing were conducted to validate signal integrity and power efficiency, making this design robust and ready for real-world applications.
Specifications: Power in a Tiny Package
This isn't just about miniaturization—it's about delivering real performance:
-
Sensor: ST VL53L5CX (Time-of-Flight, multi-zone LiDAR)
-
PCB: 8-layer with precision-matched impedance control
-
Connector: 1.27mm pitch headers for ultra-compact integration
-
Field of View: 63° x 63° (8x8 zones)
-
Measurement Range: Up to 4 meters
-
Update Rate: Up to 60 Hz
-
I²C Interface: Low-latency communication for real-time applications
-
Power Efficiency: Optimized for embedded and battery-powered systems
How to Connect and Use the LiDAR via I²C
Interfacing with this LiDAR module is straightforward thanks to its I²C communication protocol. The device operates as a slave, responding to commands from a microcontroller or embedded processor. Here’s how to integrate it into your system:
-
Hardware Connection:
-
Connect SDA (data) and SCL (clock) lines to the corresponding I²C pins of your microcontroller.
-
Use pull-up resistors (typically 4.7kΩ) on both SDA and SCL for stable communication.
-
Provide a 3.3V or 5V power supply, ensuring compatibility with your controller’s logic level.
-
-
Software Setup:
-
Initialize the I²C peripheral on your microcontroller.
-
Use STMicroelectronics' official VL53L5CX API or drivers to configure and read distance data.
-
Poll measurement data periodically or set up interrupts for event-driven sensing.
-
-
Data Processing:
-
The VL53L5CX provides an 8x8 grid of depth data, which can be used for obstacle detection, object tracking, or 3D mapping.
-
-
-
Process the raw data on an embedded system or transmit it to a PC for advanced visualization.
-
Real-World Use Cases
This LiDAR module isn't just a tech demo—it’s a game-changer for industries where size constraints meet high-performance demands:
-
Drones & Robotics: Lightweight and precise for obstacle avoidance and SLAM
-
Wearable & AR Devices: Enables 3D sensing in ultra-compact form factors
-
IoT & Smart Home: Integrates into security systems and gesture recognition
-
Automotive: Enhances driver-assistance systems with minimal footprint
A Special Thanks to EasyEDA
This project would not have been possible without EasyEDA’s incredible design tools and seamless integration with JLCPCB. Their 8-layer PCB manufacturing capabilities allowed us to realize this ambitious design, bringing ultra-compact LiDAR technology to life. From schematic capture to final fabrication, EasyEDA made it effortless.
Join the Open-Source Revolution
By sharing this project with the OSHWLab Stars community, we hope to inspire further advancements in miniaturized LiDAR. If you’re as passionate about precision hardware as we are, dive into the design files, tweak the layout, and build upon this foundation.
The future of high-performance, small-form-factor sensing starts here. Ready to take it further?
Design Drawing
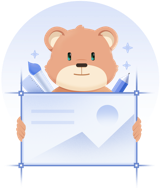
BOM
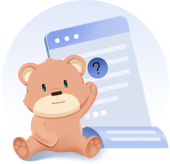

Project Members
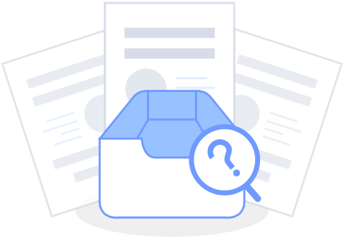
Comment