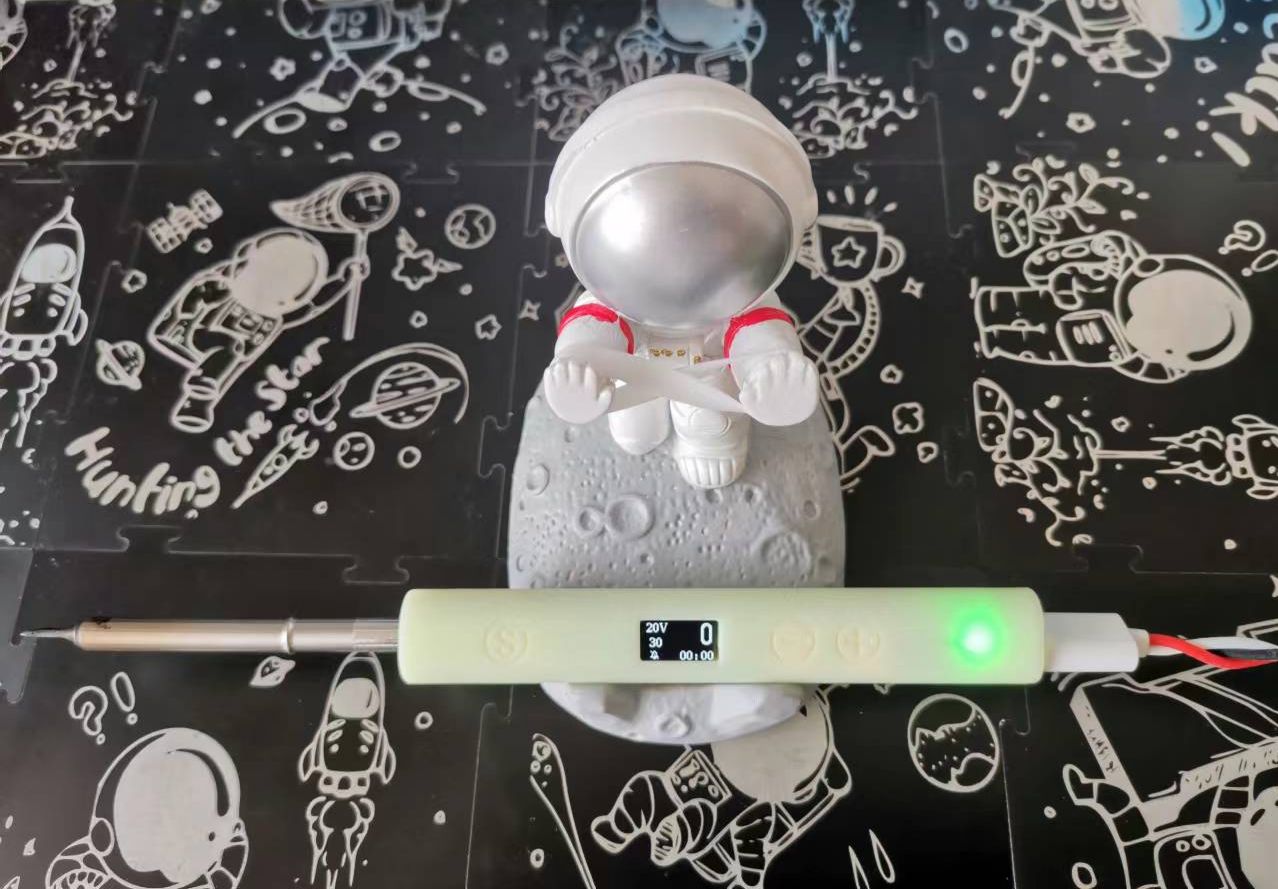
T12 welding pen v6.1
PROT12 welding pen v6.1
License
:GPL 3.0
Description
First of all, I apologize to the friends on the version of the board, because I just want to use the screen of the tuen, and did not think to open source, nor did I think that after the open source mini heating table, the friends pay more attention to my welding pen, so I made a version of 0.5 inch screen available on the market, It is convenient for interested partners to make their own electric soldering iron. Secondly, say the original intention of making the electric iron, remember more than ten years ago, the electric iron for the first time is the kind of ten pieces of external heating, and later used the internal heating type, with a long time will not touch tin, a tool is very important, I think what age, how to make the electric iron or electric iron, portable like a pen can not, I just came into contact with the T12 solver head and the small size and large power gallium nitride charger, and to have a hard core, I must give him a transparent shell, which can clearly see each component. Presumably this is the favorite of every man of science and technology, and I am looking forward to the day of large-scale application of transparent PCB.
Let's look at some model pictures next.
Finally, I highly recommend friends who like it to make one themselves. The cost will not exceed a hundred, and it is also commemorative. What you buy is a commodity after all. I am also very grateful to JLC for the service support provided, from PCB design to From prototyping, component procurement, and 3D printing, I can achieve creative freedom in front of the computer.
1 Brief description of functions
- Precise temperature control: The optimized PID parameters have fast response, small overshoot, and error of ±1°C ( only for Xi'an heads and PD65W chargers, other soldering iron heads need to be optimized );
- PD power supply : PD decoys the 20V voltage supply. Currently, only the 65W charger is tested. PD chargers with other powers are also available, but the PID parameters need to be adjusted;
- Human-computer interaction: 0.5-inch OLED simple interface, with actual temperature, set temperature, 5V/20V voltage mark, lock/unlock temperature, mute/beep switch, lock time, three touch buttons, one buzzer prompt, and power supply Indicator light, heating indicator light (PWM), +/- key touch indicator light;
- Temperature calibration: Compatible with T12 soldering iron tips of different brands, calibrated by measuring the actual temperature of five calibration points ( Xi'an tips do not require calibration ), see the operating instructions for specific operations;
- OTA update: The first time the firmware is burned through the TTL downloader, and the online update process can be implemented after connecting to WIFI. This is mainly to facilitate the update process after glue packaging.
2 Brief description of the principle
- The T12 soldering iron tip integrates a heating wire and a thermocouple that share two wires (not made by me of course) to achieve heating and temperature measurement;
- The op amp processes the thermal electromotive force generated at both ends of the thermocouple and inputs the analog quantity to the only ADC pin of ESP8266, which is converted into a temperature value through program calculation;
- PID temperature control, driving the heating wire of the soldering iron tip through PWM;
- Call the U8G2 library to drive 0.5-inch OLED through IIC;
- Obtain 20V voltage through PD deception chip and PD protocol handshake;
- Three-dimensional welding of triangular prism PCB, welding through half holes of PCB, three-sided elastic clamping is stable, and the current is sufficient.
3 Operating Instructions
- Do not touch the three touch keys before plugging in, because the touch chip is calibrated within 0.5 seconds after powering on, just hold the tail and insert the Type-C plug;
- After powering on, long touch the "+" button to unlock and you can set the temperature. The maximum program setting is 380°C, in order to extend the life of the soldering iron tip;
- Touch button description:
- Network distribution: Touch "TOUCH-" immediately after powering on to enter the network distribution mode. For the first network distribution, you need to connect to the WIFI of "T12 soldering pen distribution network" on the mobile phone. After connecting, enter the WIFI name and password to be connected in the pop-up webpage. , save, and do not need to enter it again later, unless the current WIFI cannot be connected, the network will be reconfigured;
- Temperature calibration: Immediately after power on, touch "TOUCH-" and "TOUCH+" at the same time to enter temperature calibration. There are 5 calibration points. The temperature of the soldering iron tip is measured through the external temperature sensor, and the temperature of the soldering iron tip is measured through "TOUCH-" and "TOUCH+" (temperature minus Small, increase) adjust the measured temperature value to the current value, touch "TOUCH" to enter the next calibration point, and repeat the operation until the fifth one is completed;
- Brightness adjustment: Touch "TOUCH+" immediately after powering on;
- Silent/beep switching: Touch "TOUCH-", "TOUCH+", and "TOUCH" at the same time during use. The status will be displayed in the lower left corner of the screen. The setting status will not be lost after power failure. After turning on the buzzer, there will be sound feedback when adjusting the temperature. Heating Completion reminder, startup tone;
- Lock/unlock temperature switching: Double-click "TOUCH" during use to switch, and the status will be lost after power failure. When the temperature is not locked, if you touch "TOUCH" with your thumb to heat, the temperature cannot be adjusted (to prevent accidental touch), otherwise the heating will stop; after locking the temperature, even if you do not touch "TOUCH", it will heat, and the temperature cannot be adjusted, and the timer is 5 minutes. (The duration can be modified in the program code) and then restart to prevent the danger from forgetting to turn off the power.
4 Things to note
In view of the pitfalls that I have encountered during the production process and the problems that my friends may encounter, I have sorted them out. There may be some that I have not considered. Friends can write them in the comment area and we will promptly respond after seeing them. Reply, I don’t plan to set up an exchange group at the moment, because I still have school work, and I don’t have the energy to do it for the time being, so I will write it in as much detail as possible so that novices can make it according to the tutorial. Attached is the link to the previous version of the tutorial video https ://www.bilibili.com/video/BV1Wq4y1Y7PS?share_source=copy_web
- Main component preparation
Component name | Things to note |
Shrapnel | The raw material is the pole piece of the CR1220 battery holder. You need to use scissors and pliers to modify the shape. |
0402 SMD 4.7uf capacitor | Be sure to choose one with a voltage resistance of 25V. |
Buzzer | SMD 5020 Passive SMD Buzzer. |
26M crystal oscillator | SMD3225-4P, pay attention to the direction when welding, there is a triangular notch on pin 1. |
Four indicator lights in series with resistors | Currently it is 470Ω. You can also change it to other suitable resistance values, but the brightness will be different. |
4.7uH power inductor | The model is SWPA252012S4R7MT. You can choose LCSC C87640 or Taobao. |
0.5 inch OLED | You can find it on LCSC and Taobao, 88*48 CH1115 driver IIC. |
Main control chip | When choosing esp8266, you need to solder W25Q32. When choosing esp8285, you don’t need to solder. It is recommended to use 8285 to save money. |
Touch chip | Compatible with TTP223 and PT2042AT6. |
Precision operational amplifier | Compatible with GS8551 and SGM8551XN5G/TR in SOT-23-5 package. |
- Soldering and PCB depaneling
You can solder the whole board first and then separate the board with a hook knife, but be careful not to cut the circuit. You can also separate the board first and then solder it individually. This method is recommended for novices . Weld the components of the front patch first, then weld the buzzer and female base on the back, then weld the spring piece, and finally weld the screen. When welding the screen, the FPC solder joints should be small.
After each board is powered on and tested correctly, perform three-dimensional welding of the triangular prism. First, insert the three boards into the auxiliary positioning block for positioning. Adjust the position. Weld the half hole at the tail first. It is best not to weld it firmly at once, leaving some The room for adjustment is like tightening multiple screws. Don't tighten one at a time. Apply a little tin first, and then add more tin to solder it firmly after the triangular prism structure is determined.
- Compile and burn
Use Arduino to burn the program. Before that, you need to compile it and add library files, otherwise there will be a compilation error. First install the development board library of ESP8266. I uploaded the offline installation package (8266_package_2.7.4.exe) in the attachment. Just double-click to run it. After installation, restart Arduino and select the development board, as shown in the figure below. If you are using 8285, select For 8285, use 8266 for 8266. There is a difference between the two when burning.
Install the library file, as shown in the figure below. Add the .ZIP library in the attachment. You can also click Manage Library and search for online installation.
After the compilation is successful, burn it. Use a TTL downloader to connect to the onboard TX, RX, 3V3, and GND. I used a homemade ESP8266 downloader. I aimed it at the four solder points and pressed and held for burning. Anyway, I only used it once. OTA will be used for subsequent burning. Before burning, enter the download mode. Use tweezers to short-circuit the two solder joints of IO0 and hold them. At the same time, use another tweezers to short-circuit the two solder joints of RST and then disconnect them. Then disconnect the short-circuit of IO0. Then the burning begins.
- Shell making
The original design was to use a disposable glue package as the shell. The biggest advantage of this is that it is small in size and hard-core cool. However, it is troublesome to make. It requires a silicone mold and sealing. It takes several days to solidify and the success rate is also very low. Later, It also needs to be polished, and the touch buttons should be used under sealed conditions (this is also a pit). So I took a step back and tried to 3D print a detachable shell if it is not transparent. Although there are also transparent materials, I don’t recommend it for friends who don’t have a printer (I asked one shop and it cost 100+). I first made a sample, made of white photosensitive resin, mainly to test whether the size would fit, as shown in the picture below.
Sure enough, the inner cavity is a bit big, but that's not a problem. Just make some modifications. Now that our school is closed, we don't have a printer and the express delivery is super slow, so there is no opportunity for iterative modifications. I hope that friends with stereolithography printers around me can help. I verified it (see the attachment for the STL file). It is not recommended to use an FDM printer because it has a thin wall and a slender shaft structure. The hot bed attached to the bottom is not strong and the surface accuracy is not high, even though I increased the bottom attachment area. The shell printing model is shown in the figure below. It contains two parts, the shell and the shell cover. In order to increase the attachment area during printing, an auxiliary circular plate is added to the shell. It can be cut off after printing is completed.
I also tried to place an order on 3D Monkey and chose URT6180 photosensitive resin and PA12 nylon as shown in the picture. I did not choose white because it was too ordinary.
- Touching the problem (filling the hole you dug yourself)
In the past, the shell sealed with glue was in direct contact with the touch pad, so as long as a capacitor with a suitable capacitance value was used, a suitable touch sensitivity could be achieved. However, there is an air medium between the detached shell and the touch pad, so the capacitor is Adjusting the capacitance value to the minimum and the highest sensitivity is far from enough. This will result in the touch pad inside being unable to be touched through a layer of shell (it's over, that's not useless). Fortunately, a medium was finally found - nanometer Traceless glue (single-sided), cut a piece of suitable size and stick it on the touch pad to reduce the gap between it and the shell, which perfectly solves the problem of touch capacitance.
5 Update Instructions
- 2022-04-26 Verify the replacement screen and modify the display part of the program;
- 2022-05-02 Use the professional version of JLC EDA to redraw the schematic diagram and PCB; upload the Gerber file and place an order directly with JLC for free, and the BOM table will be placed in the JLSC with one click (Note: Some components are temporarily out of stock. It was still in stock when I started drawing the schematic, but it was gone when I uploaded the tutorial 😂);
- 2022-05-13 Verify the compatibility of the PCB drawn by the professional version, ESP8266, PT2042, and GS8551, conclusion: completely 👌;
The professional version of EDA comes with welding auxiliary tools . In the upper right corner of the open source project - open the editor, open the PCB file, tools - welding auxiliary tools;
Reminder: The welding difficulty is indeed a bit high, so it is normal to fail the first time. Try it a few more times. It is recommended that the circuit be welded in modules and tested while welding;
- 2022-05-20 The printing shell verification is completed. You can print with a standard size shell. There is no need to use a larger version. See the attachment for the effect video; To solve the touch problem, use copper foil tape to increase the touch pad area, as shown below:
Designed by _buerchen (from OSHWHub)
Design Drawing
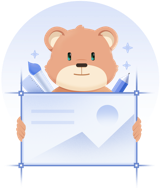
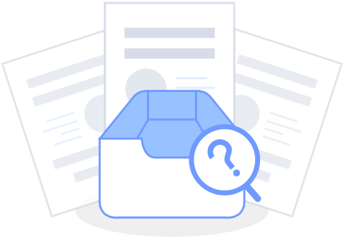
Comment