Silicon carbide totem pole 3KW power supply.
Input specification: AC 110V~270V 20Amax
Output specification: DC 350V-430V 20Amax
Power: 3000W (Design Power: 3500W)
Efficiency: 98.5%
This power supply is the pre-PFC link of the subsequent 3KW LLC power supply or full-bridge adjustable power supply.
The introduction of this design is more detailed, please read carefully, and at the same time, if there is something wrong, please criticize and correct, like the collection will select a friend in the comment area to send a set of PFC totem pole finished board!!
1. Introduction to the principle of PFC
1.1 What is PFC?
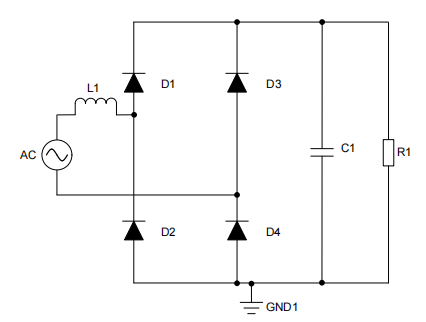
To understand PFC, we must first define the power factor. The power factor is the ratio of the active power to the apparent power in watts. Active power is the power consumed by the load, and apparent power is the power that cycles between the source and the load. The ideal power factor is 1, which means that there is no loss due to reactive power and all apparent power is active power. Switching power supplies are often used for power factor correction. Switching power supplies typically utilize diode bridges to rectify alternating current (AC) signals to direct current (DC) signals. This diode bridge choppers the AC signal, affecting the power factor and total harmonic distortion (THD).
Figures 1-1 and 1-2 show the waveform of a system with power factors of 1 and 0.69. Note that a decrease in the power factor leads to an increase in peak current.
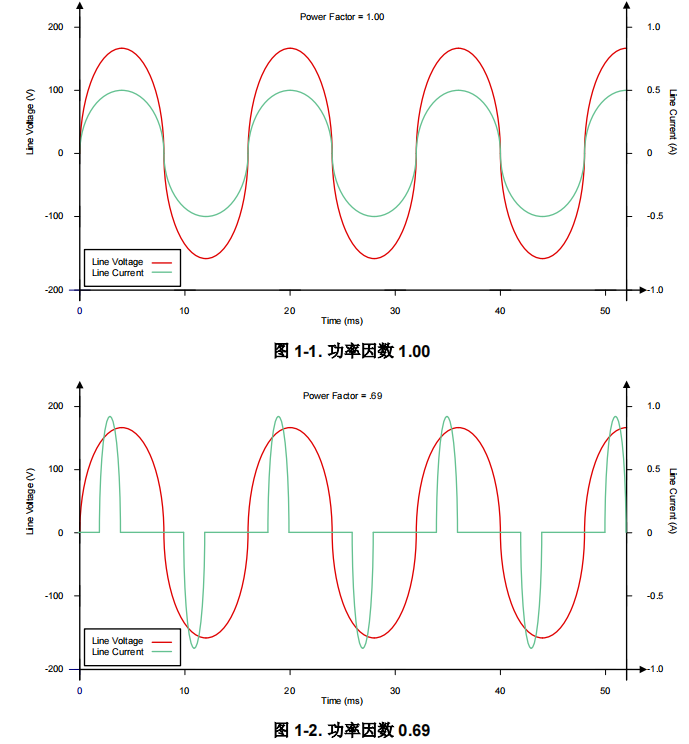
Switching converter topologies are used for active power factor correction to improve power efficiency and density. One of the most outstanding topologies of the last two decades has been the boost PFC, which uses a single low-side MOSFET, an inductor, and a diode. In order to achieve efficient AC/DC conversion, MOSFET gate drivers must meet specific requirements in order to drive the MOSFET effectively. Some of the requirements for these drivers include peak drive current and switching characteristics.
Since PFCs require high-power switching, they require high drive currents. Fast switching characteristics such as rise and fall times and propagation delay enable fast switching transitions, reducing losses and increasing efficiency. The reason for the need for fast switching transitions is the switching losses in the MOSFETs. Because they can handle dynamic voltages and currents, MOSFETs are inefficient during turn-on and turn-off. Other requirements include undervoltage lockout and noise handling capability. Boost PFCs are typically driven by single-channel, low-side, non-isolated gate drivers, as shown in the figure below.
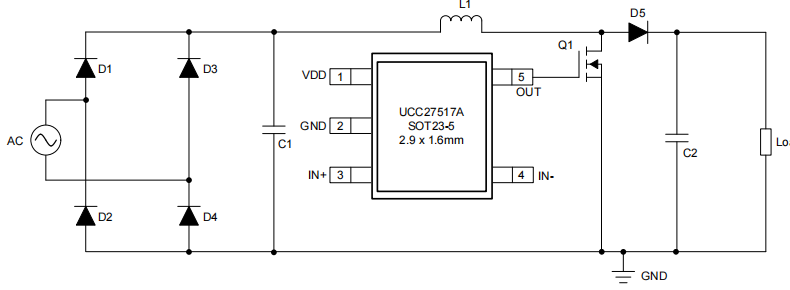
1.2 Why is PFC used in switching power supplies?
Relevant countries stipulate that PFC must be added to electrical equipment that exceeds a certain power to improve the quality of the power grid, if PFC is not added, it will affect the overall efficiency waveform of the power grid, etc., resulting in other users can not be used normally, the power factor (PF) is a measure of the degree of effective use of electricity, the larger its value, the higher the power utilization rateAs a kind of capacitive input circuit, the phase difference between current and voltage of the switching power supply will lead to the loss of switching powerIn order to reduce this loss and improve the efficiency of power utilization, a PFC circuit is introduced into the switching power supplyBy improving the power factor of the power supply, the PFC circuit can effectively manage the reactive power while consuming active power, thereby reducing unnecessary losses on the grid and improving the overall efficiency of the power system.
1.3 What are the different forms of PFC?
Staggered boost PFC is a more efficient and complex option than traditional boost PFC. Staggered boost PFC increases system efficiency but increases component count.
The gate driver requirements for an interleaved boost system are very similar to those for a boost system, except that the second MOSFET requires an additional channel. To drive the two MOSFETs required for this topology, a dual low-side gate driver, such as a UCC27624, is typically used. The following diagram shows an example of a staggered boost circuit.
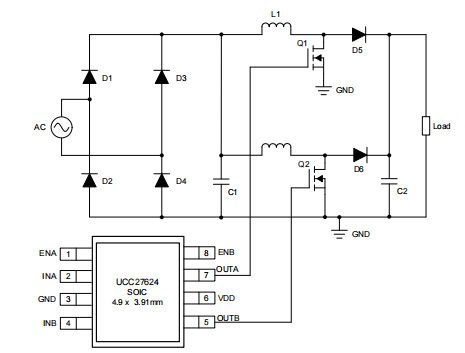
Due to the development of the third generation of semiconductors, totem-pole bridgeless PFC began to be widely used.
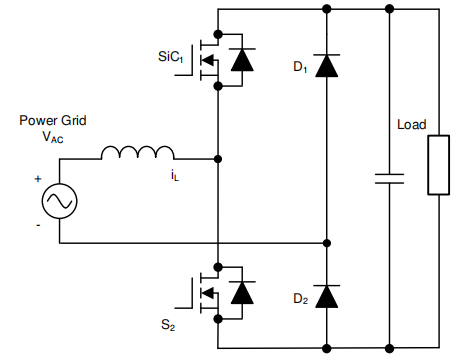
Conventional PFC converters implement a passive diode bridge for rectification, a technique now known as passive PFC technology. The advantages of this type of solution are simple design, high reliability, slow system control loop, and low cost. However, the disadvantages are also obvious: the passive components are heavy, have a low power factor, and generate significant power losses, resulting in large heat sinks and large heat dissipation. Further investigation revealed that on low-voltage lines for wide power applications, the input bridge consumes approximately 2% of the input power. If the designer can suppress one of the series diodes, they can save 1% of the input power, increasing the efficiency from 94% to 95%. Due to the above shortcomings, the power rating of conventional PFCs in bridge is limited to less than a few hundred watts, especially in hybrid electric vehicles (HEVs) or electric vehicles (EVs), where small space and low weight are key design parameters. As a result, there is a growing trend towards bridgeless architectures that eliminate traditional diode bridges. OBC is based on silicon power devices, which have limitations such as low efficiency, low power density, and high weight. With the advantages of SiC MOSFETs, designers can take advantage of the superior performance of fast switching, low reverse recovery charge, and low RDS(ON) to dramatically improve these limitations.
1.4 Why can Totem Pole PFC high-frequency tubes only use GaN and SiC, but not ordinary MOS?
The inherent problem in the totem pole PFC is the operating mode transition at the AC voltage zero crossing. When the AC input changes from a positive half to a negative half at the zero crossing, the duty cycle of the low-side high-frequency switching SiC2 changes from 100% to 0%, and the duty cycle of SiC1 changes from 0% to 100%. Due to the slower reverse recovery of the high-side diode (or the body diode of the MOSFET), the cathode voltage of D2 cannot immediately jump from ground to DC positive (which results in a large current spike). Due to this issue, designers are unable to use Si MOSFETs in continuous conduction mode (CCM) totem-pole PFCs.
Therefore, SiC1 and SiC2 must be gallium nitride (GaN) or SiC MOSFET field-effect transistors (FETs) with low reverse recovery, and for this project, we chose SiC.
1.5 What is the direction of the working current of the totem pole PFC?
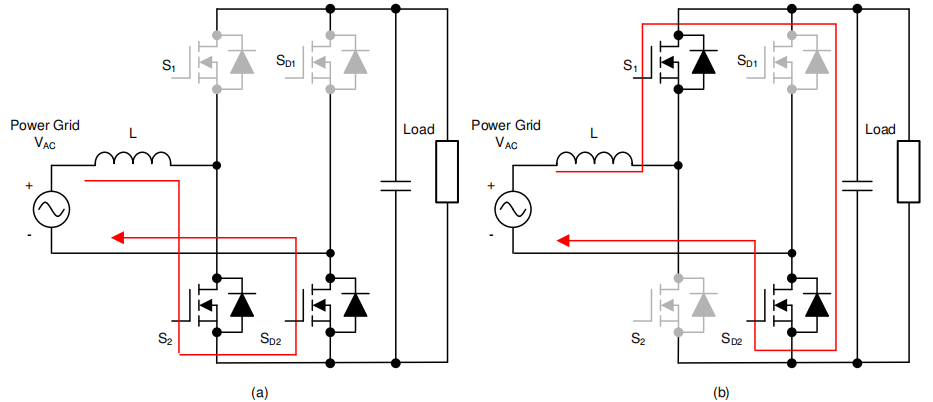
Totem-pole bridgeless PFC operation in the positive half-cycle: (A) when S2 is on and (B) when S2 is off
Totem-pole bridgeless PFC operation in the negative half-cycle: (A) when S1 is on and (B) when S1 is off
High-frequency GaN FETs operate at a switching frequency of 65kHz, and a pair of Si MOSFETs operate at a power frequency (approximately 45Hz to 60Hz). Therefore, the conduction path includes a GaN switch and a low-frequency Si switch, and the conduction loss is significantly reduced. Dual-channel interleaving technology is used to reduce on-loss and input current ripple. The test results show that the efficiency is more than 98.5%.
1.6 What is the wave logic of totem pole PFC (CCM) and how to solve the zero-crossing spike?
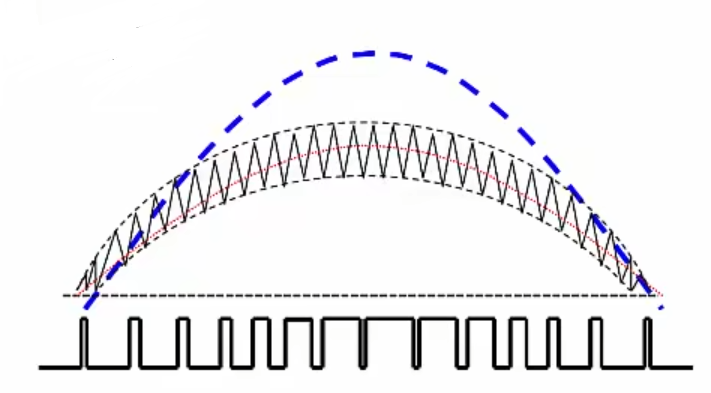
Wave logic: In the positive half cycle of the AC current, the main PWM goes from low duty cycle to high duty cycle, and then back to low duty cycle, so that the inductor current presents a sine wave, and the slave tube complements each other in the opposite direction. However, the totem pole PFC has the problem of zero inductor current commutation spike, and in order to improve the current waveform, special treatment is required at the zero crossing point.
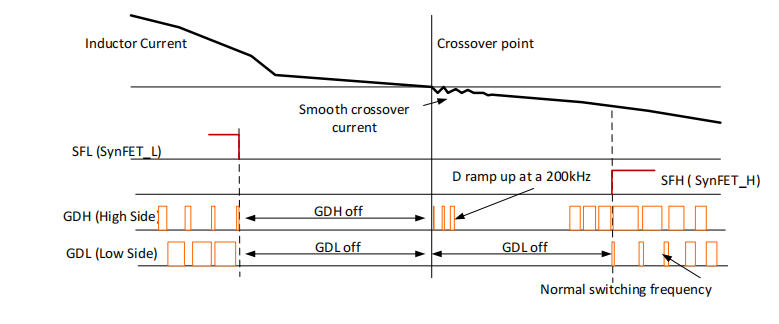
The figure above shows the totem pole drive waveform, GDH and GDL are the high-frequency tube drive waveforms, SFL is the low-frequency tube drive waveform, Inducor Current is the inductor current, and Crossover point is the zero crossing point.
The outputs of all four gate drive GDL/GDH/SFL/SFH are turned off before the zero crossing, and after the zero crossing, the active tube (SFL or SFH) of the high frequency tube starts working first. Instead of starting with a full duty cycle output, the active tube's duty cycle starts from zero and gradually increases to full duty cycle at a PWM frequency of 200kHz until the end of dead time. In this way, the HF can smoothly switch between the active and passive states. The soft start of the active tube produces a very smooth inductive current to discharge the parasitic capacitance at the midpoint of the low-frequency bridge arm, which minimizes or eliminates current spikes at the AC zero crossing. LF synchronous transistors are typically superjunction MOSFETs whose Coss stores a lot of energy, resulting in large zero-crossing current spikes. The zero-crossing dead time is ±100us, which prevents potential short circuits when the AC sampled signal is close to 0V and may be interfered with by noise.
1.7 What is the difference between PFC working modes?
There are two main working modes of PFC, CRM (Critical Conduction Mode) and CCM (Continuous Conduction Mode), and CRM is widely used in occasions with low power of about 300W.
The main features of the CRM model PFC are as follows:
Power switch zero current conduction: In CRM mode, the power switch is turned on in the case of zero current, which helps to reduce switching losses and improve efficiency.
Inductor current rises linearly: When the switch is turned on, the inductor current rises linearly
Higher Conducted Interference Low Frequency Band: Although the controller using the CRM PFC can easily modify the feedback part, this approach will result in higher conducted interference in the low frequency band
Changeable Switching Frequency: CRM mode allows the switching frequency to be changed at the zero span of the sine wave and can make the switching frequency very high, but usually the upper limit of the frequency is imposed within the IC to prevent EMI testing from failing.
CCM is widely used in high-power occasions
A distinctive feature of the CCM mode is that the transmitted current flows continuously, almost DC, and the ripple is very smallThis continuously flowing inductor current helps to reduce switching noise and improve the efficiency and stability of the power supplyCompared with DCM mode, CCM mode is more suitable for high-power occasions.
2. Introduction of silicon carbide and design of positive and negative power supply
2.1 What is Silicon Carbide?
Silicon carbide MOS tubes use silicon carbide (SiC) semiconductor materials, while ordinary MOS tubes use silicon materials. Silicon carbide has excellent properties such as high melting point, high hardness, high thermal conductivity, high radiation resistance, and high temperature stability, while silicon materials do not have these properties
In terms of characteristics, the switching speed of silicon carbide MOS transistors is faster, which can achieve higher frequency and higher efficiency power conversion. It has higher electric field strength and lower on-resistance, better anti-electromagnetic interference performance, and is suitable for high-temperature, high-power, high-frequency and high-voltage applications.
In terms of working principle, the silicon carbide MOS tube has a higher electric field strength and a higher leakage current, and the conduction loss will be smaller under high voltage conditions. The working principle of ordinary MOS transistors is based on the substrate injection concept or induction concept, while silicon carbide MOS transistors have higher electric field strength and switching speed.
2.2 Why does silicon carbide need to be driven by positive and negative power supplies?
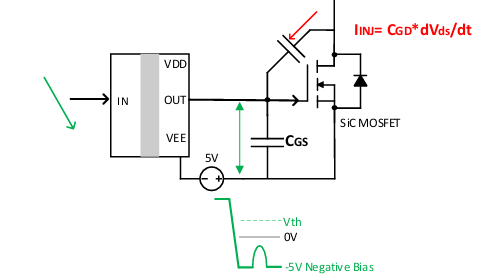
The application scenarios of SiC MOSFETs in OBC DC/DC systems are mostly high-voltage and high-switching rates, so the dVds/dt at switching time is significantly higher than that of ordinary Si MOSFETs. Taking a bridge circuit as an example, when the top tube is quickly turned on and the bottom tube is turned off, the Vds of the bottom tube will increase, and the charge will be transferred to the gate of the bottom tube through the Miller capacitor Cgd, which will cause a small spike in the gate voltage. Depending on the manufacturer and channel technology, the threshold voltage of a SiC MOSFET is typically 2V to 5V. If the voltage rise caused by crosstalk during this process exceeds the threshold voltage for the SiC MOSFET to be turned on, it may cause the lower side arm to be turned on by mistake, which may lead to the upper and lower bridge arms going straight through, causing serious consequences such as system short circuit damage.
In order to avoid the risk of bridge arm pass-through during the switching process, the SiC MOSFET usually needs to use positive and negative voltage drive, that is, through negative voltage shutdown to ensure that even if there is a small voltage spike during the shutdown process, the threshold voltage will not be exceeded to cause the MOSFET to turn on.
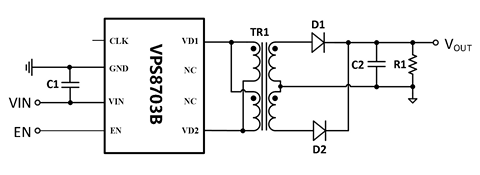
This project uses VPS8703B full-bridge driver chip, VPS8703B is a transformer driver specially designed for small size, low standby power consumption of micro-power isolated power supply, its periphery only needs to match simple input and output filter capacitors, isolation transformers and rectifier circuits, can achieve 6~30V input voltage, a variety of output voltages, output power 1~10W isolation power supply. The maximum input voltage is 30V, which is a maximum input voltage of 5V compared to the SN6505 of Texas Instruments, which can accommodate a wide input voltage range, and the internal frequency of 250Khz is integrated. Isolated positive and negative power supplies can be obtained through the transformer output windings, and can also be used to supply power to isolated current sampling and voltage sampling chips.
2.3 Why should the auxiliary power transformer be capacitor at the beginning?
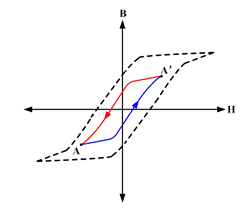
The normal operation of the full-bridge transformer needs to meet the requirements of "volt-second balance", that is, the volt-second product generated by the transformer excitation process should be equal to the volt-second product generated by the demagnetization process. If they are not equal, core saturation may occur. where B is the magnetic flux density of the core, and H is the strength of the magnetic field inside the core. When the switch PM1 and NM2 are turned on, the full-bridge transformer is in the "excitation" stage, and the magnetic flux density will continue to increase along the arrow direction from A to A', and the magnetic flux density will reach the positive maximum value A' when PWM1 and PWM2 are turned off, and when the switch PWM2 and PWM1 are turned on, the full-bridge transformer will be in the "demagnetization" stage, and the magnetic flux density will continue to decrease along the arrow direction from A' to A, and the magnetic flux density will reach the negative maximum value A at the time of PM2 and NM1 shutdown. The magnitude of the magnetic flux density B is mainly determined by the product of the voltage amplitude Vp of the primary winding of the transformer and the turn-on time Ton of the switch during the turn-on process, that is, Vp*Ton, which is usually called the "volt-second product". The normal operation of the transformer requires that the principle of "volt-second balance" is satisfied, that is, the volt-second product generated by the transformer excitation process should be equal to the volt-second product generated by the demagnetization process. As the converter continues to work, the accumulation of bias energy will eventually lead to the magnetic flux density of the core gradually increasing in the direction of the bias and exceeding the saturation magnetic density range of the magnetic element, and eventually lead to the saturation of the core and the failure to work normally.
In a word: no DC-blocking capacitance may lead to bias of magnetism, bias of magnetism will lead to magnetic saturation, magnetic saturation will lead to a sharp increase in current, burning the device, VPS8703 of course, with overcurrent protection, you can not add capacitance, adding capacitance may lead to a decrease in output voltage and power.
2.4 Why isolate drives?
As a semiconductor integrated circuit (IC), an isolation device allows data and power to be transmitted between high- and low-voltage units while preventing any dangerous direct current or uncontrolled transient currents from flowing out of the grid. A well-known example is lightning strikes. Ground loops formed in circuits with high energy flow can be broken by isolation. There are several methods of isolation. Of all the isolation methods, galvanic isolation is one that provides protection against large potential differences.
2.5 How to choose a silicon carbide MOS tube?
It is necessary to pay attention to the selection of silicon carbide models, Ciss, Corss, Qg and other parameters, due to the high switching frequency of silicon carbide, so these parameters will affect the switching loss of silicon carbide, and Ron determines the conduction loss, when using the driver, we should also pay attention to the driving current, carefully calculate, and select the appropriate Rg opening resistance and shutdown resistance.
The driver IC generally charges and discharges the gate capacitor by source current and sink current, so as to realize the switching of MOSFET or IGBT. In order to achieve the fast switching characteristics of SiC MOSFETs to achieve lower switching losses and higher switching frequencies, higher drive currents are often required.
By looking at Vgs and Vds, we can determine whether the value of Rg is reasonable.
There is a noticeable delay at the top of the rising edge of Vgs in the image above, where the Rg is too large.
The above figure shows the waveform after adjusting Rg, there is neither overshoot nor delay, overshoot will exceed the maximum gs voltage of silicon carbide, but the time is generally very short, silicon carbide can also work, but the working life will be reduced, in some silicon carbide data sheets have pointed out the working time of overvoltage.
The figure above shows the relationship between the turn-on loss and the value of Rg, and the next section will describe how to calculate Rg in detail.
3. Theoretical calculations
3.1 The value of the current limiting sampling resistance
The right resistance value can bring a reasonable range of power protection, pay attention to the power of the resistor
3.2 Calculation of inductance value
It is worth noting that the inductance of the inductor should be 70% when the inductance is offset at 20A DC, pay attention to the inductance specification, this project uses a 360uh inductor, and there is an inductance of 320uH at 20A.
3.3 Output capacitance calculation
Try to choose multiple parallel connections for the output capacitors, and remember to calculate the power of the bleeder resistor, and add a 100nF decoupling capacitor at the output end to reduce high-frequency ripple
3.4 Calculation of MOSFET driving resistance
The drive resistor can be adjusted according to the waveform, and 10 ohms is recommended.
3.5 Calculation of switching loss and conduction loss
In PFC hard switching, the switching loss and conduction loss are the same in small and medium power occasions (1-10kW), and when the high power is more than 10kW, the conduction loss dominates, because the synchronous rectifier ZVS is turned on and off. Due to the very low frequency of the power frequency, the conduction loss is dominant. Switching losses are related to the Vds rise and fall times as well as the frequency.
3.6 Inductor core loss calculation
At present, there are many ways to calculate the core loss, the most important is the Steinmetz formula and the loss formula given by the core manufacturer for material testing, which is generally fitted.
The hysteresis loop of H (B is the magnetic flux density, H is the magnetic field strength) of the core material is a function of frequency/'. The total loss of the iron core is composed of three parts: hysteresis loss, eddy current loss and residual loss, and the residual loss at high frequency mainly includes the loss caused by size resonance, domain wall resonance and natural resonance_l but its proportion is not large. It can be seen from the dynamic hysteresis loop that the higher the operating frequency, the larger the hysteresis loop, and the greater the loss per unit mass. When the loss separation method is used to describe the core loss of a transformer, it can be decomposed into static hysteresis loss, dynamic eddy current loss and residual loss P.
The loss density of the core (in w/kg) represents the loss per unit mass of the core, and the classic method to describe the loss density of high frequency is the Steinmetz formula.
where K is the loss coefficient, f is the frequency, B is the magnetic flux density, and a and β are the loss constants.
3.7 Compensated zero pole calculation
This circuit uses a type two compensator to compensate, there is a zero point and a pole, because the output voltage has 2 times the power frequency ripple, so the voltage sampling crossing frequency I set is 5Hz, to reduce the impact on the circuit voltage loop. In the previous project, when the voltage of the 220/380V adjustable power supply was set, it was found that when the voltage was set below 5V, the output of EG1163S was unstable, and the Vgs waveform appeared large and small waves, and the traversal frequency and phase margin of the loop were tested, the loop response was reduced, the phase margin was increased, and the 10nf feedforward capacitance was changed to 20nf to solve the problem of unstable voltage regulation.
4. Waveform analysis
High-frequency tube waveform
Voltage and current waveforms
High-frequency tube waveform
Low-frequency tube waveform
5.Physical display
The maximum temperature of 3KW for 10 minutes is the inductance temperature, 34.6 degrees
The maximum temperature of 3KW for 120 minutes is the inductor temperature, 43.8 degrees
The maximum power is 3.5kW and can be operated for a long time
The efficiency curve is around 98%.
At this time, the internal resistance of the power frequency tube is 60mΩ, the internal resistance of the high-frequency tube is 27mΩ, and the ciss is 2nF
The power frequency tube is replaced with 30mΩ internal resistance, and the high frequency tube remains unchanged, and the test results are:
3000/(231.2*13.15)=0.98675
Efficiency increased from 98% to 98.675%
Then replace the high-frequency silicon carbide, replace it with 15mΩ internal resistance, ciss 9nF, and change the driving resistance Rg to 4.7Ω, which has been tested.
3000/(230.8*13.25)=0.981, an extra 18W loss
Reduced efficiency from 98.675% to 98.1%.
Physical drawing
References
【1】律方成,郭云翔. 非正弦激励下中频变压器铁损计算方法对比分析[J]. 高电压技术,2017,43(3):808-813. DOI:10.13336/j.1003-6520.hve.20170303016.
【2】席彬晟. 纳米晶铁心中频变压器振动和损耗特性研究[D]. 湖北:三峡大学,2023.
【3】采用 C2000 和 GaN 的 4kW 单相图腾柱 PFC 参考设计,德州仪器
【4】适用于电器的 4kW GaN 图腾柱 PFC 参考设计,德州仪器
【5】采用 GaN 的 7.4kW 电动汽车/混合动力电动汽车双向车载充电器参考设计,德州仪器
【6】如何调整碳化硅 MOSFET驱动减少功率损耗,意法半导体
【7】OBC DC/DC SiC MOSFET驱动选型及供电设计要点,德州仪器
【8】碳化硅栅极驱动器:电力电子行业的颠覆性技术,德州仪器
Comment