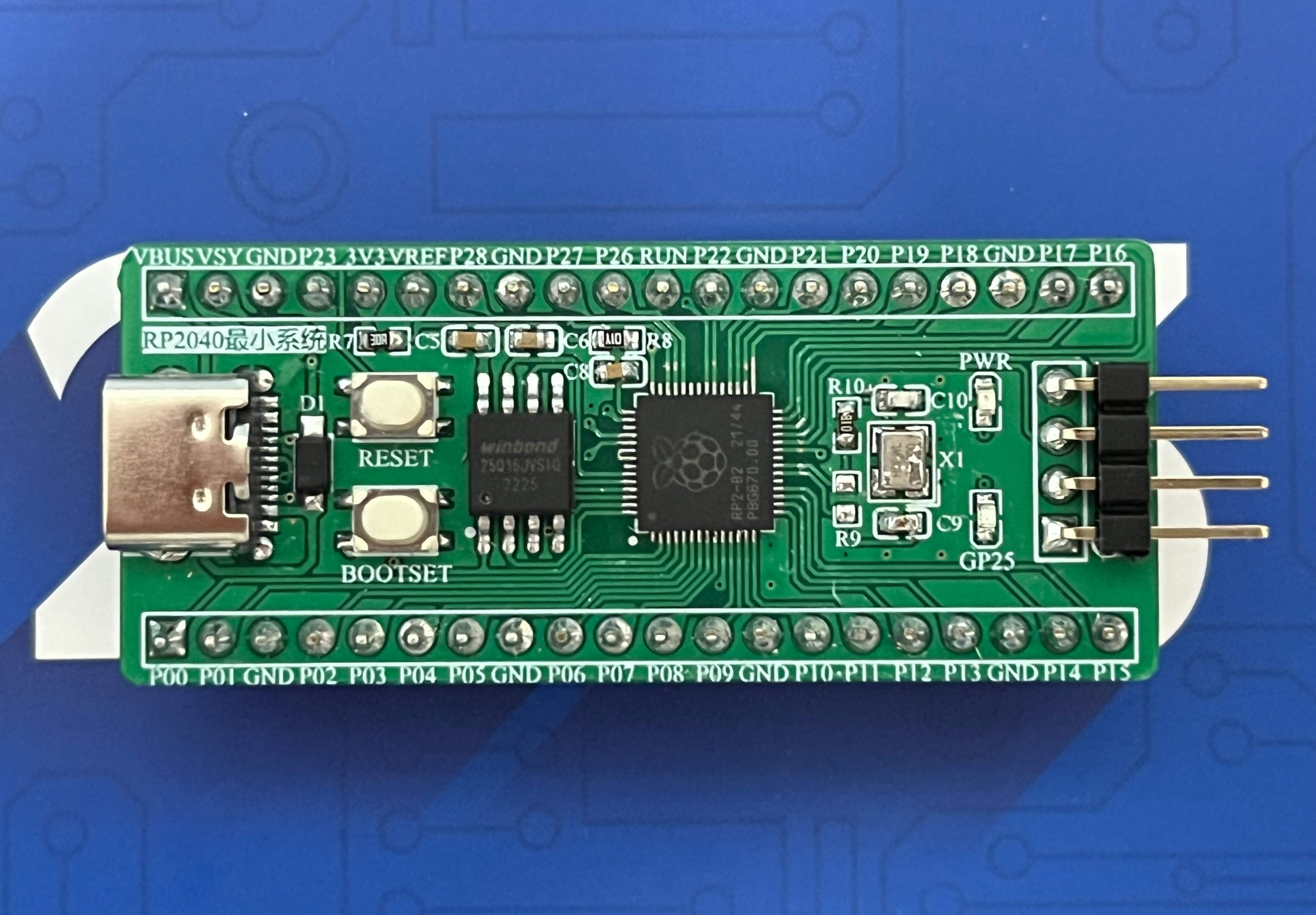
[ Core board ]RP2040 minimum system
PRO[ Core board ]RP2040 minimum system
346
0
0
0
Mode:Full
License
:GPL 3.0
Creation time:2025-02-21 03:30:34Update time:2025-02-24 02:49:22
Description
Designed by 立创EDA课程案例推荐 (from OSHWHub)
Link:https://oshwhub.com/course-examples/he-xin-ban-rp2040-zui-xiao-xi-tong
Design Drawing
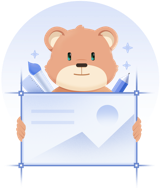
Add to Album
0
0
Share
Report
Followers0|Likes0
Related projects
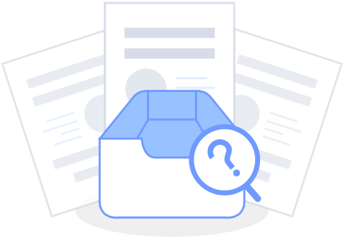
Comment