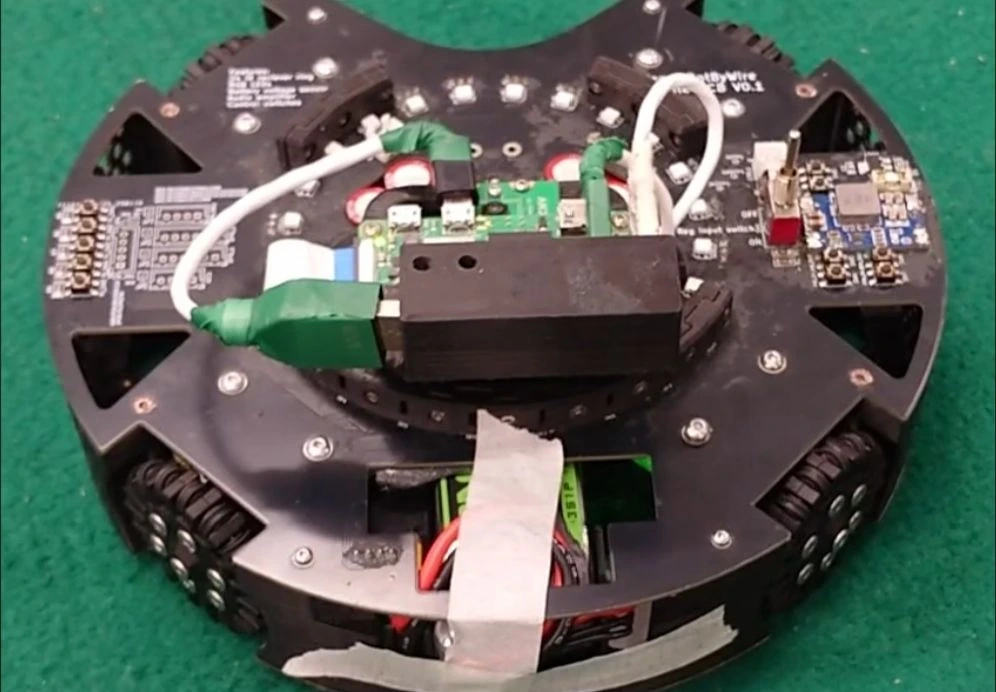
robot sensor base
License
:MIT License
Description
This project is an open source, highly lightweight base with many integrated sensors, for a 4-omniwheel robot. The design features a compact yet versatile platform incorporating mounting points for four omni wheels in a standard X configuration, providing holonomic movement capabilities in any direction.
The PCB-integrated base includes dedicated mounting holes for DC motors, with the motors positioned at 45-degree angles for optimal force distribution. The geometry of the PCB is designed to be lightweight while remaining rigid while carrying the load of the rest of the robot.
Sensors and controller
Two optical mouse sensors (specifically, the PMW3360, interfaced through SPI) are strategically placed on opposite sides of the base, enabling precise position and rotational tracking.
A ring of 16 downward-facing ambient light sensors (ALS-PT19) paired with corresponding LEDs provides comprehensive ground sensing capabilities, useful for line following, edge detection, or surface analysis. The sensors are arranged in an octagonal pattern around the base's perimeter for maximum coverage.
This combination of sensors enables the robot to be adapted to any competition environment.
At the heart of the system is an ESP32 microcontroller, offering both WiFi and Bluetooth connectivity options. The microcontroller controls all the motor drivers (which are external), mouse sensors and samples the ambient light sensors. This single microcontroller can form a closed-loop system that reliably responses to surface features, ensuring optimal robot performance.
Power is supplied to sensors and microcontroller via a Mini560 3.3V regulator, which is affordable and accessible, and highly efficient. An optional 5V source can be supplied externally, and level shifters plugged into the circuit, to shift the motor driver control voltages to 5V to be compatiable with more motor drivers.
Circuit protection
Power is supplied via an XT-60 plug, that is commonly found on 3S LiPo batteries used in robotics competitions. The board features reverse polarity, overvoltage and overcurrent protection, using a standard zener-thyristor circuit that provies reliable reverse polarity and overvoltage protection while not harming efficiency. A fuse is used to quickly break the circuit when the reverse polarity protection triggers, and can be manually replaced. Overcurrent protection is achieved with a lower-rated polyfuse, that will reset itself after tripping, reducing manual work needed to fix the robot when something goes wrong. With many slots available to configure values for bypass capacitors, a good capacitance can be achieved to filter out noise and voltage spikes from the power source. This greatly reduces the chance of damage to the robot due to human error or oversights, which can save valuable time and money.
Omniwheel
As a critical part of the robot, it is very important that they are durable and able to withstand impact without breaking.
However, plastic small omniwheels which incorporate many rollers (to increase uniformity) are often prone to breakage, as the arms in between the rollers are very small, and can easily snap when the wheel impacts something else. To solve this problem, a metal outer layer for the omniwheel is developed to provide structural support and shield the inner plastic layer from impact. This has been designed to be CNC machined and mounted onto a 6mm hex shaft, though the design can be adapted to your needs.
This is a 5mm diameter omniwheel designed to house 18 rollers, using a steel wire to hold all the rollers in place.
Material choice
The material of choice for the omniwheel is 7075 aluminium, which has very high tensile strength, as the material for this omniwheel, the wheel can be made very lightweight while making sure that the outer layer protects the omniwheel from breaking. With JLC CNC's high precision machining services, a good fit with the rollers and motor shaft can be ensured, keeping the system rigid and much less likely to break. This wheel provides low maintenance and reliable high performance, making it ideal for optimising robots and reducing points of failure.
Manufacturing
The CNC omniwheel front can be manufactured out of either 6061 or 7075 (recommended) aluminium, through JLC CNC service. The omniwheel backing and rollers are designed to be 3D printed or CNC machined (for maximum reliablility), either through FDM (abs, nylon, and other more durable materials recommended), or through SLA (tough, engineering resins recommended). They can also be manufactured through JLC 3DP service to have parts guarenteed to work and reduce manual labour. If CNC machining them, 7075 aluminium is recommended (especially for the rollers).
Thanks to the generous support from OSHWLabs for the fabrication of the PCBs and the wheels, the project has been successfully completed! Below is a YouTube video demonstrating the robot:
https://www.youtube.com/watch?v=L6MNduiWscc
Design Drawing
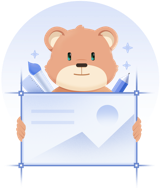
BOM
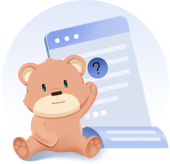

Project Members
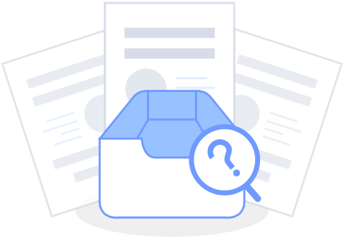
Comment